Electrical Testing
Acceptance Testing (New Construction)
These are tests that are performed to NETA Testing specification on new electrical equipment, usually after installation, prior to energization. Here’s a detailed look at why it is essential:
-
Verification Against Design and Specification:
These tests are performed to determine whether a piece of equipment is in compliance with the purchase specification and design intent.This includes verifying that the components are suitable for their intended application and are installed according to the manufacturer's recommendations. -
Functional Testing:
This involves testing the equipment under various operational conditions to ensure that it functions as intended. This may include testing under normal operating conditions, as well as under simulated fault conditions to verify that protective devices and systems react appropriately. -
Mechanical Damage:
Acceptance tests are also valuable in ensuring that the equipment has not been subjected to damage during shipment or installation.

-
Mechanical Damage:
Acceptance tests are also valuable in ensuring that the equipment has not been subjected to damage during shipment or installation. -
System Integration Testing:
Checks that all parts of the electrical system work together as intended. This is crucial in complex installations where different systems need to interact without interference.
-
Documentation and Reporting:
Accurate documentation of test results is critical. This includes detailed records of the testing procedures used, the results obtained, and any anomalies or non-conformities observed. These documents are essential for both compliance purposes and for future maintenance or troubleshooting.
Preventive Maintenance Testing
Maintenance testing of electrical equipment involves routine inspection, testing, and servicing of electrical systems and components to ensure continued safe operation, reliability, and efficiency. This type of testing is a critical component of any preventive maintenance program. Here’s a detailed look at why it is essential:
-
Safety:
Perhaps the most critical aspect, maintenance testing helps prevent accidents and ensure the safety of personnel by identifying and correcting potential hazards like electrical shorts, faulty wiring, or degraded insulation before they lead to accidents or injuries. -
Functional Testing:
This involves testing the equipment under various operational conditions to ensure that it functions as intended. This may include testing under normal operating conditions, as well as under simulated fault conditions to verify that protective devices and systems react appropriately. -
Reliability:
Regular testing and maintenance improve the reliability of electrical systems, reducing the likelihood of unexpected breakdowns and interruptions to operations. -
Cost Savings:
By identifying and fixing problems early, maintenance testing can prevent costly repairs and equipment replacements later. It also helps extend the lifespan of electrical components -
Compliance:
Compliance: Maintenance testing ensures compliance with national and international safety standards and regulations, which can include OSHA regulations, NFPA standards, and local electrical codes.
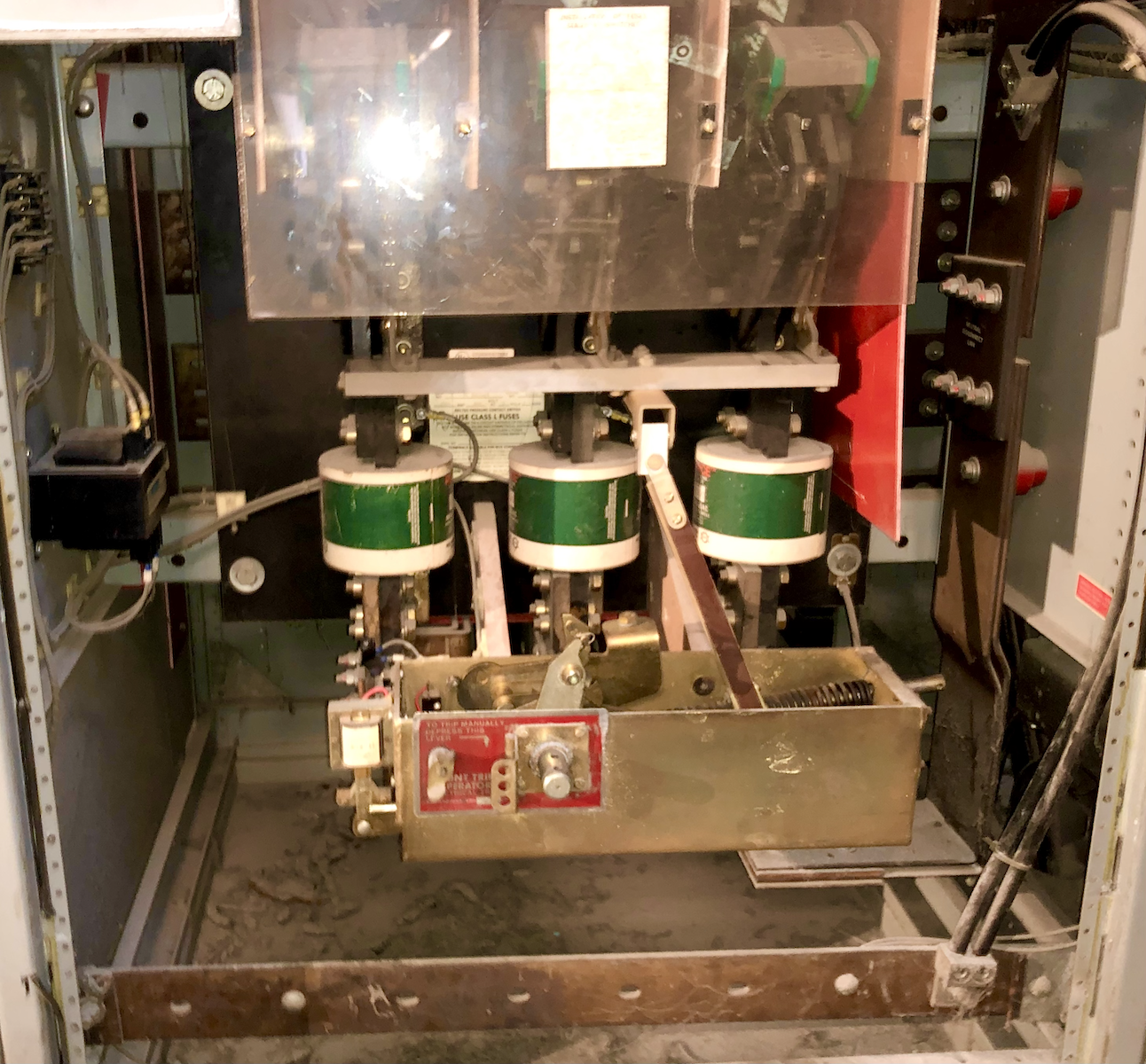
-
Efficiency:
Properly maintained equipment operates more efficiently. For instance, clean and well-maintained connections have lower electrical resistance and use less energy, which can lead to energy savings. -
Documentation and Improvement:
Maintenance testing provides a record of equipment performance over time. Analyzing this data can help predict failures and optimize maintenance schedules.
Electrical Preventive Maintenance Program (EPM)
EPM consists of the following essential elements:
- Designating qualified and responsible personnel
- Regularly scheduled inspection, testing, and servicing of equipment
- Survey and analysis of electrical equipment and systems to determine maintenance requirements and priorities.
- Programmed routine inspections and test reports so that proper corrective measures can be prescribed
- Performance of necessary work
- Concise but complete records
Planning an EPM:
The following factors should be considered in planning an EPM
-
Personnel Safety
Will an equipment failure endanger or threaten the safety of any personnel?
What can be done to ensure personnel safety? -
Equipment Loss:
Is installed equipment-both electrical and mechanical-complex or so unique that required repairs would be unusually expensive? -
Production Economics:
Will breakdown repairs or replacement of failed equipment require extensive downtime?
How many production dollars will be lost in the event of an equipment failure?
Which equipment is most vital to the production?
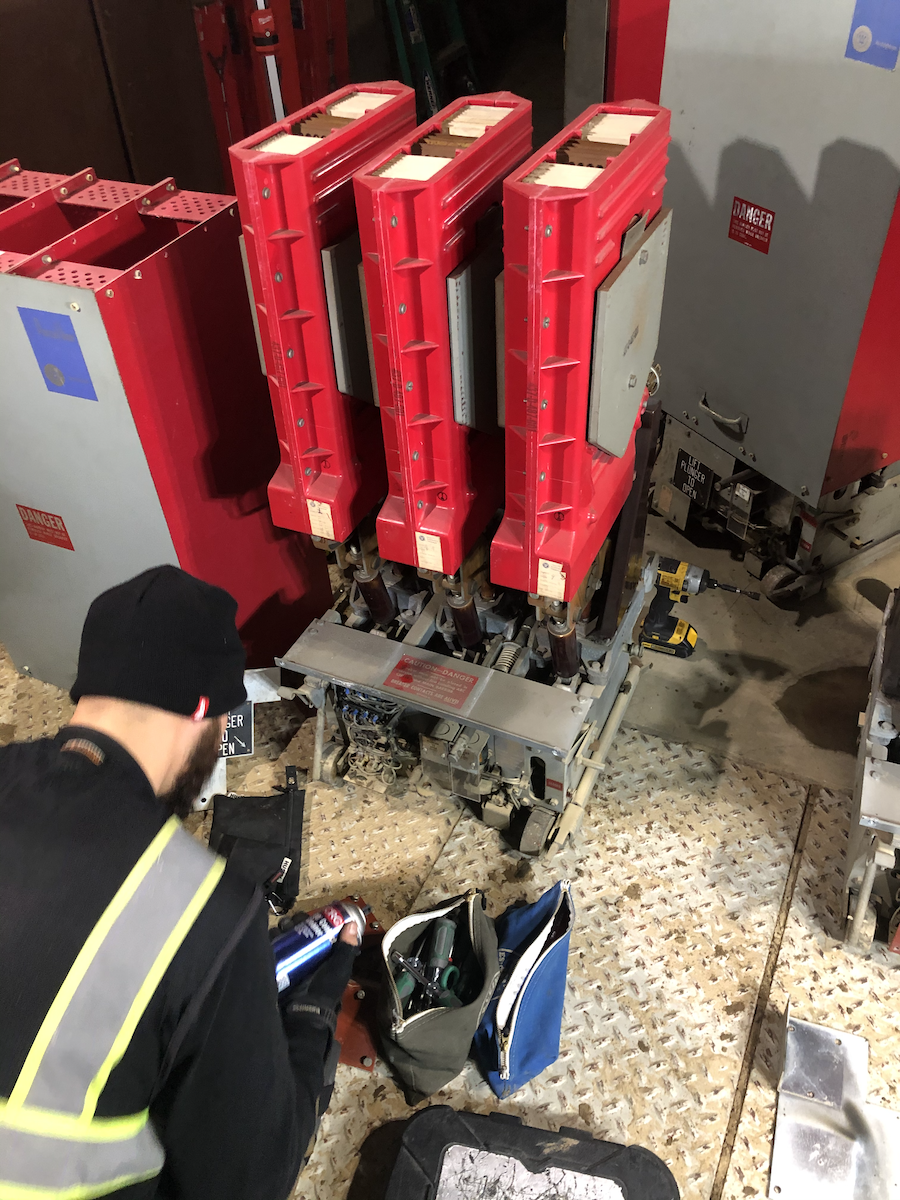